Related Articles
QC With An ERP Module
Quality control of QC in short is a process by which the quality of all the factors involved in the production of a good or the provision of services is inspected and reviewed. The output of the goods and services are reviewed in line with and compared against ideal company parameters and product quality aim. We can begin to understand how critical and crucial of a component quality control for a production-based or service-based organization as quality of products and services are a way to communicate loudly to the customer base. Quality deficiencies can break a company and quality efficiencies and most definitely make a company.
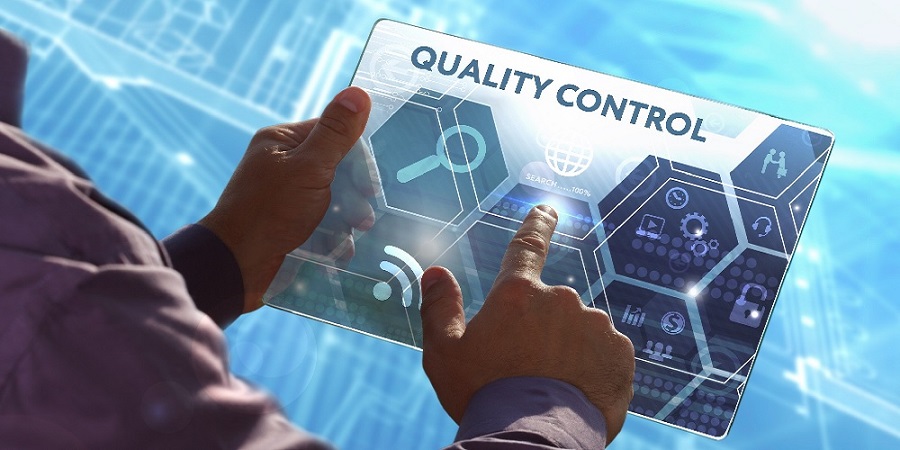
QC is quite literally a company’s way of life and its critical position in a company’s framework means that it has to be designed, introduced, and led by top management. Most companies’ quality control measures fail because top management executives do not spend sufficient focus and energy behind these measures. ERP systems have proved themselves to be one of the most powerful tools at executives’ disposal for proper quality control management. The basic characteristics of good quality control management include:
- Customer-sourced data response.
- Top management leadership.
- Constant improvement of products, services, and the production process.
- Fast response.
- Action based on factual data.
- Employee participation.
All these are things ERP system modules bring to the table for overall prosperity of a company in terms of growth and definitely in terms of improving quality.
INCORPORATING ERP SYSTEMS INTO THE QUALITY CONTROL PROCESS
If you are to formulate an effective quality control strategy and procedure roadmap, you will rely on results and insights taken from data that has integrity and is of good quality. Studies of shown that a criminally low percentage of companies collect data that is of acceptable quality standards which means that a great many quality control plans around the world lack a proper punch to truly make inroads and be effective. From the barebones basics, your company should have a quality baseline that is required to be met, and this baseline should be regularly updated and modified with incorporation of real data.
The collection of data and maintaining their quality is a key area where ERP systems can come into use. The latest advances in business software technology allows many ERP systems to log data instantaneously within an user-friendly interface. This automatic collection and sorting of data ensures that you save time and a lot of trouble collecting data across various partners, customers, and suppliers, empowering you to instead focus your on growing your business and improving the quality of your products and services. Real-time data availability is also important as you would do well to continually look for ways to keep improving quality, staying ahead of your contemporaries.
Consistency is another key aspect of a good quality control scheme. This is achieved through the standardization of materials, products, and procedures and it is key to running a successful business. Regardless of the industry your company is in, raw materials are brought in from an outside source and the confidence of trust is often not enough to ensure that all raw materials that you buy are all of the same high standards. Certain ERP modules can be used to set up a system of inspections that you can refer to in order to create a quality checklist that reviews all raw materials before they received the stamp of approval and are sent to the production line. An ERP system can keep track of all information based on key performance indicators that you can set and present the information in a user-friendly interface.
In case an issue occurs, data used by the ERP can help it track the origin of the issue specifying the product batch and sort any quality control issues using the information the system is continually being fed. An all-encompassing ERP solution across your company will remove inter-departmental clutter that can quite easily exist and ensure that all departments are working towards meeting the same quality standards. Last but not least, standardization ensures that all production line workers have the right set of guidelines for manufacturing products consistently.
Compliance to industry standards is undoubtedly important in maintaining quality insurance. Every industry has its own basic quality standards that manufacturers must adhere to in order to even stay afloat, and many of these same industries have to abide by strict regulatory requirements mandated by the law. A robustly designed ERP system is built with industry compliance in mind, built in to the process. As a result, you can use your EPR solution as a reference for all the information you may need in order to amend your process.
CONCLUSION
Remember that a quality management strategy means the production of a higher quality product and ultimately, happier customers down the line. There exist a wide range of different methods of measuring the performance, such as quality control charts that depict whether sampled products or processes are meeting their intended specifications or not and if not, by what degree. The Taguchi Method is also another method of quality control which emphasizes the roles of research, design, and development in order to mitigate the frequency of defects and failures in products. It is a method that puts greater importance on the pre-development design process, above the manufacturing process in its different approach to quality control in order to eliminate defects before they can occur.
ERP systems definitely allow you to incorporate these methods to full effect to create your quality control maxims and then make sure that they are enforced. You may even try your hand at making your own set of quality control maxims keeping in mind the company’s goals, top management’s decisions, and your own principles.
Syncoria is a digital transformation company based in Canada and an official Odoo Ready partner.