Related Articles
Reduce costs in mass production. One of the challenges of modern industries is reducing costs without cutting corners in product designs. This means that quality must not be compromised for lowering production costs. In mass production systems, where raw materials are bought in bulk and there are multiple assembly lines that streamline into one linear procurement system to amplify the number of goods being produced, this poses a greater problem as any missteps or incorrect strategies will result in errors across all the channels, affecting each and every product. Thus, time is lost for damage control and effectively costing the firm significantly in profit margins.
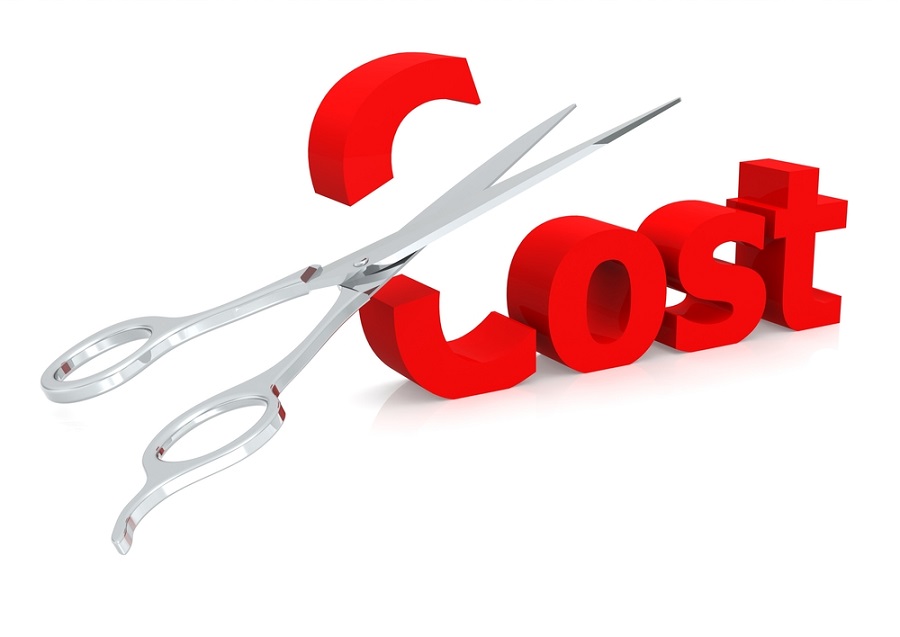
Reduce Costs in Mass Production
The majority of the cost (75%) lies in material costs and labor. Buying individual components, designing systems in maintaining and refining them, employing the right number of workers to handle the parts and providing them with adequate training – all require a proper scheme to be made which requires frequent updates depending on consumer demands and which cannot be executed without the right tools. Thus, we will now look at different methods of expenditure reduction for both raw materials and the workforce.
Reducing material costs
- Change the design of your product. Redesign your product to reduce the overall price of the finished good. This can be done by analysing which components are the most expensive and negotiating with the respective suppliers to lower prices. An effective way of doing this is knowing what prices other suppliers are offering and hinting to bring changes in the supply chain. This will force the supplier to give in to your desired price.
Another way of driving down prices by strategically rethinking the product is by removing certain parts which are not critical for maximum consumer satisfaction. For example, components with secondary functions such as packaging may be removed altogether. This is especially helpful for online businesses which rely on e-commerce and are often seen to not print logos unless they want to boost sales. Tweaking the product in such a way is called value engineering and it requires a strategic approach in removing non-value added processes such as transportation. - Apply the principles of lean manufacturing. Lean manufacturing is based on the singular principle of keeping waste to an absolute minimum. Seven types of waste must be dealt with: overproduction, inventory, conveyance, correction, motion, processing and waiting. By creating an inventory which is mass-customized, products are only built when they are ordered and this is predicted by the demands in the market. This means goods are not overproduced. By correct moving of the product so that they are not sent back to the production line, products and workers can simultaneously move in a linear fashion which increases efficiency by saving time lags drastically.
- Negotiate with your suppliers. As mentioned previously, negotiations with your suppliers are fruitful in optimal reduction of costs. One way to approach a supplier is to enter into long-term agreements where you lose flexibility over changing suppliers and are bound by a contract to exclusively get raw materials from them. In the long run, this loss in flexibility allows should be compensated by the benefits of a lower final price.
Suppliers of ancillary services may also be regionalized, i.e. they are geographically closer to your production site. While this is a difficult task to achieve, if it can be done, this drives down transportation costs and provides a smoother vertical integration. With some hefty incentives offered as part of the negotiation, suppliers may choose to simply relocate at an area closer to your factory.
Reducing labor costs
- Utilize part-time labor and limit the use of overtime. Full time employees get bonuses, shares of profits and other fringe benefits such as housing and cars as well. These costs can be removed once you hire more part-time labor. Reducing overtime is also a smart way to reduce costs; often under pressure overtime seems like a good way of rapidly increasing production, the increased costs slowly chip away at the profits, thinning profit margins further.
Hiring “on-call” workers – employees who come to work when they want to make money – is helpful as well, as they are paid lower wages due to lesser working days and they tend to be highly specialized in their fields, so training costs are also reduced. - Automate processes as much as you can. The internet of things(IoT), AI engaged widely in deep learning skills and the increased use of robots in manufacturing simply go on to show how rapid advancements in technology have reduced the need for the human touch in refining, developing and assembling the individual parts of a product. Automated inspection and identification of parts saves plenty of time wasted by humans and are also less prone to errors, so the likelihood of damage control will be drastically lower. An automated system, even though it requires a significant investment, has an extremely positive return in the long run in terms of operational costs.
The key benefit of having an automated system is that it can update information in cloud-based networks where all the data of the organization is stored. In fact, most businesses opt in for an enterprise resource planning(ERP) solution, which identifies and removes bottlenecks in production by analyzing the workflow. In most ERP suites, various modules are integrated to reduce overhead costs of the firm, such as strategic network optimization, advanced supply chain planning, employee and inventory management and electronic kanban systems. These all help to simplify the supply chain, monitor worker performance and analyze which goods are still in the inventory and which assets are retired.
There are many management software which offer ERP solutions. We recommend using Odoo. Odoo is a user-friendly business software that provides you with just about every tool you would ever need. Built under the same UI, Odoo uses multiple modules mentioned above to create a cohesive flow of information within one conduit so that analyzing the data on different areas of expenditure and creating a budget accordingly becomes faster and easier. With servers all around the world, Odoo should be the perfect pick for your business. Syncoria, a digital transformation company based in Canada, is an official Odoo Ready partner. To contact Odoo, call at +1 (416) 628-5522, or email them at [email protected].